Aluminum "6061"
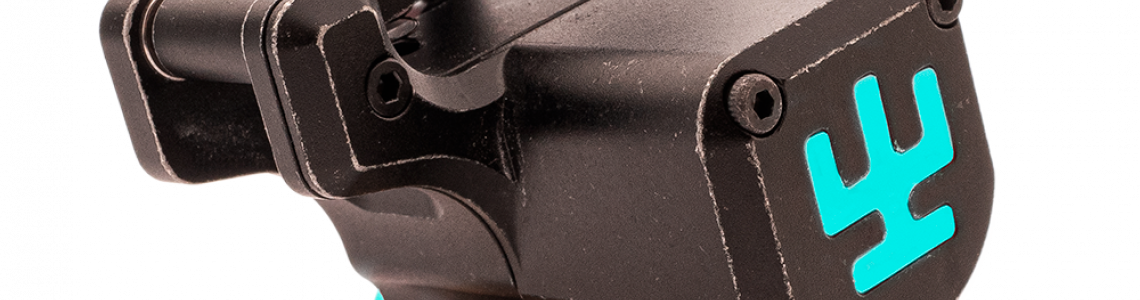
Aluminum 6061 is one of the most widely used aluminum alloys in the world—and for good reason. It offers an excellent balance of strength, corrosion resistance, weldability, and machinability, making it incredibly versatile across a wide range of industries. From aerospace to construction, from automotive parts to structural components, 6061 aluminum is the go-to choice for engineers and manufacturers looking for performance and reliability.
What makes 6061 truly exceptional is that it's not just a single metal—it's an aluminum-magnesium-silicon alloy with a carefully engineered composition that enhances its performance dramatically compared to pure aluminum.
Table of Contents
Chemical Composition
Aluminum 6061 is classified as an aluminum-magnesium-silicon alloy under ISO 209-1. The alloying elements each contribute specific benefits to the overall material properties:
- Al (95.8–98.6%): Lightweight, corrosion-resistant, and conductive.
- Mg (0.8–1.2%): Primary strengthening element; increases strength and corrosion resistance.
- Si (0.4–0.8%): Improves castability and enables heat treatment.
- Fe (up to 0.7%): Enhances structure stability but reduces conductivity.
- Cu (0.15–0.4%): Boosts strength with Mg and Zn; affects corrosion resistance.
- Cr (0.04–0.35%): Counters iron’s effects, strengthens welded joints.
- Zn (up to 0.25%): Reinforces strength when combined with Mg and Cu.
- Ti (up to 0.15%): Refines grain and reduces cracking.
- Mn (up to 0.15%): Increases strength and heat resistance.
Mechanical and Physical Properties
- Density: 2.70 g/cm³
- Tensile Strength (T6): 290 MPa
- Yield Strength (T6): 240 MPa
- Elongation at Break: 8–10%
- Modulus of Elasticity: 68.9 GPa
- Thermal Conductivity: 167 W/m·K
- Corrosion Resistance: Excellent
- Weldability: Very good
- Machinability: High
- Heat Treatability: Suitable for heat treatment
Explore Vlad Blad Tattoo Machines
Advantages and Disadvantages
Advantages:
- High strength-to-weight ratio
- Excellent corrosion resistance
- Good weldability and machinability
- Versatile in forming and extrusion
- Widely available and cost-effective
Disadvantages:
- Lower strength than 7075 in high-load applications
- Reduced corrosion resistance with copper content
- Not ideal for high wear-resistance needs
Applications Across Industries
Automotive and Transportation
- Body struts and structural components
- Chassis and cargo systems
Aerospace and Defense
- Hydraulic tubing and minor load-bearing parts
- Used in Space Shuttle fuselage and Hubble telescope antenna beam
Construction
- Extruded frames, panels, and railings
- Used in facades and high-yield strength structures
Marine
- Boat structures and dock components
- Offshore drilling platform tubing
Bicycles and Sports Equipment
- BMX and road bike frames
- Climbing gear and sporting goods
Chemical Industry
- Storage tanks and containers
- Resistant to acids, alcohols, and ammonium nitrate
Global Equivalents and Standards
- USA (AA/ASTM): 6061
- Europe (EN AW): EN AW-6061
- Germany (DIN): AlMg1SiCu
- Japan (JIS): A6061
- Russia (GOST): АД35 (approx.)
- China (GB): 6A02 (close equivalent)
Supply Forms and Processing
Aluminum 6061 is commonly available in:
- Extrusions: bars, rods, angles, channels
- Sheets and plates
- Pipes and hollow sections
- Forgings and rolled products
Common temper: T6 (heat-treated and aged). Others include T4 and T651.
Processing methods:
- CNC machining
- Extrusion and rolling
- Anodizing and painting
- TIG and MIG welding
Conclusion
Aluminum 6061 is an ideal solution for engineers and manufacturers seeking a reliable, high-performance material. Its strength, versatility, and corrosion resistance make it one of the most trusted aluminum alloys on the market. Whether in aerospace, marine, construction, or everyday products—6061 continues to deliver results professionals can depend on.
8 Comment(s)
1
1
1
1
1
1
1
1
1
1
1
1
1
1
1
1
1
1
1
1
1
1
1
1
1
1
1
1
1
1
1
1
1
1
1
1
1
1
1
1
1
1
1
1
Leave a Comment