What to do if the spring often breaks?
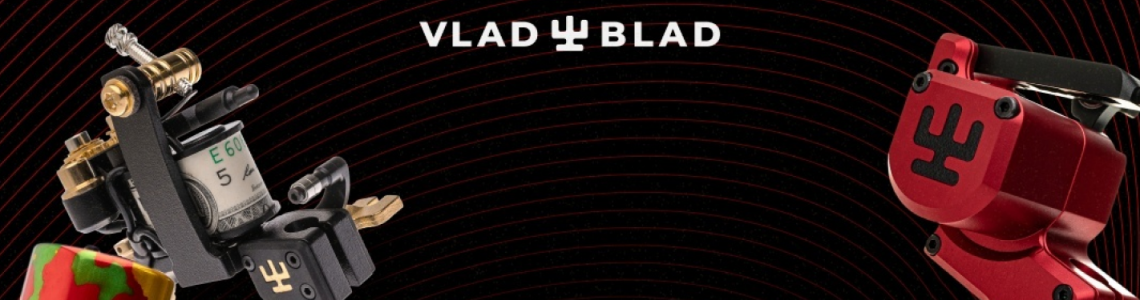
Let’s be honest: a broken spring can feel like a serious letdown — especially when it happens on a premium machine. But before you start thinking something’s wrong with your tattoo machine, let’s take a deeper look.
At Vlad Blad, we build high-powered, high-performance tattoo machines. That’s our DNA. Our machines deliver strong, consistent hits — and with that power comes more stress on internal components like springs. It’s not a design flaw. It’s physics.
Table of Contents
- Let’s Be Honest: Why Springs Break
- The Real Reason? It’s the Power
- What We've Done to Solve It
- Explore Vlad Blad Tattoo Machines
- Still Breaking Springs? Here’s What You Can Do
- Why One Spring Breaks Fast, and the Next Lasts Years
- Our Promise to You
- Conclusion: High Performance Comes With High Standards
- Frequently Asked Questions
The Real Reason? It’s the Power
Some brands sell machines that feel smooth but are actually quite weak. Springs in those machines aren’t loaded as heavily, so they rarely break. But that comes at the cost of performance. Our machines are built for serious tattooing — they hit harder, penetrate better, and deliver the results pros expect.
More power = more vibration = more pressure on the spring. That’s why even if you’ve never had a spring break on other machines, it might happen once or twice on a Vlad Blad.
And that’s okay — because we’ve already thought this through.
What We've Done to Solve It
- Tested dozens of spring steels from the USA, Europe, China, and Russia.
- Tried every manufacturing method imaginable: punching, laser cutting, waterjet, and electric discharge.
- Built our own CNC electrical discharge machine to precision-cut our springs in-house.
- Developed a proprietary process for cutting, bending, and stabilizing the spring material.
- Introduced factory-bent springs so you don’t have to adjust them every time.
- Invented the monolithic spring design — now widely adopted in the industry.
We’re also the first and maybe only company to offer free spring replacements within the first year. If your spring breaks — even twice — we’ve got you covered.
Explore Vlad Blad Tattoo Machines
Still Breaking Springs? Here’s What You Can Do
1. Avoid Rust at All Costs
Moisture is the enemy. Rust creates microscopic weak spots that can become break points under pressure. Wipe down your spring after every session and store your machine in a dry place.
2. Monitor Amplitude
More amplitude = more stress on the spring. Some artists increase amplitude instead of properly adjusting needle protrusion. That’s a recipe for disaster.
Pro tip: The needle should stick out 1–2mm when the machine is idle. This way, you get better control without abusing the spring.
Why One Spring Breaks Fast, and the Next Lasts Years
Sounds weird, right? But here’s the thing — spring steel is not 100% uniform. Even high-quality, high-carbon steel can have internal stresses in specific points. On a weaker machine, these go unnoticed. On a powerful Vlad Blad machine? They can crack under pressure.
That’s why sometimes:
- The first spring breaks after a few sessions.
- The second breaks again — annoying!
- The third one? Works like a champ for 5 years straight.
It’s not you. It’s metallurgy. And we’re constantly improving.
Our Promise to You
We’re not just building machines. We’re building a relationship with every artist who chooses Vlad Blad. That’s why we:
- Offer 7-day-a-week support via phone or Facebook.
- Replace broken springs for free during the first year.
- Continuously upgrade our spring manufacturing to minimize failure rates.
You’re not alone — and your machine isn’t “broken.” It’s just doing its job at a higher level than most.
Conclusion: High Performance Comes With High Standards
If you’re pushing boundaries in your work, you need a machine that does the same. That’s where Vlad Blad comes in. Yes, a spring might break. But that’s because your machine is powerful — and we’ll always be here to support you when it happens.
Frequently Asked Questions
Why do springs break more often on Vlad Blad machines?
Because our machines are stronger. More power = more stress on the spring.
How do I prevent spring breakage?
Avoid rust and manage your amplitude. Make sure your needle sticks out 1–2 mm at rest.
Is spring breakage covered under warranty?
Yes! We offer free spring replacements for the first year.
What should I do if my spring breaks twice in a row?
Don’t worry — it’s rare, but it can happen. Contact us and we’ll send you a new one. The next one might last for years.
8 Comment(s)
1
1
1
1
1
1
1
1
1
1
1
1
1
1
1
1
1
1
1
1
1
1
1
1
1
1
1
1
1
1
1
1
1
1
1
1
1
1
1
1
1
1
1
1
Leave a Comment